top of page
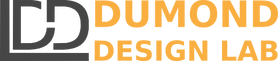
Machine Condition Monitoring
Our Machine Condition Monitoring projects are designed to provide comprehensive, real-time insights into the performance and health of your industrial machinery.
We believe our Machine Monitoring System-related research could enhance productivity, reduce operational costs, and ensure the seamless operation of your machinery.
Structured Data Ontology for AI in Industrial Asset Condition Monitoring
Jacob Hendriks, Mana Azarm, Patrick Dumond
2024
This paper proposes an ontology for prognostics and health management (PHM) applications involving sensor networks monitoring industrial machinery. Deep learning methods show promise for the development of autonomous PHM systems but require vast quantities of structured and representative data to realize their potential. PHM systems involve unique and specialized data characterized by time and context, and thus benefit from tailored data management systems. Furthermore, the use of dissimilar standards and practices with respect to database structure and data organization is a hinderance to interoperability. To address this, this paper presents a robust, structured data ontology and schema that is designed to accommodate a wide breadth of PHM applications. The inclusion of contextual and temporal data increases its value for developing and deploying enhanced ML-driven PHM systems. Challenges around balancing the competing priorities of structure and flexibility are discussed. The proposed schema provides the benefits of a relational schema with some provisions for noSQL-like flexibility in areas where PMH applications demand it. The selection of a database engine for implementation is also discussed, and the proposed ontology is demonstrated using a Postgres database. An instance of the database was loaded with large auto-generated fictitious data via multiple Python scripts. CRUD (create, read, update, delete) operations are demonstrated with several queries that answer common PHM questions.
University of Ottawa Constant and Variable Speed Electric Motor Vibration and Acoustic Fault Signature Dataset
*Mert Sehri, Patrick Dumond
2024
Induction motors are used in industry as they are self-starting, reliable, and affordable. Applications for these motors include lathes, mills, pumps, power conveyor belts, and commercial electrical and hybrid vehicles. Induction motors have various types of failures, including rotor unbalance, rotor misalignment, stator winding faults, voltage unbalance, bowed rotor, broken rotor bars, and faulty bearings. There is a need for differentiating mechanical faults from electrical fault signals when identifying what part of the motor needs maintenance while using machine learning. Therefore, data collection is essential for electric motor fault diagnosis. The University of Ottawa Electric Motor Dataset – Vibration and Acoustic Faults under Constant and Variable Speed Conditions (UOEMD-VAFCVS) is provided to address this issue. Data from accelerometers, temperature, and acoustic sensors are collected to provide quality electric motor fault data. The dataset includes various induction motor faults useful for time domain analysis. The high-quality data provided by this dataset will help facilitate the differentiation between mechanical faults and electric faults when using fault detection methods, which is a valuable asset for machine condition monitoring.
University of Ottawa constant load and speed rolling-element bearing vibration and acoustic fault signature datasets
*Mert Sehri, Patrick Dumond, Michel Boutchard
2023
The collection and analysis of data play a critical role in detecting and diagnosing faults in bearings. However, the availability of large open-access rolling-element bearing datasets for fault diagnosis is limited. To overcome this challenge, the University of Ottawa Rolling-element Bearing Vibration and Acoustic Fault Signature Datasets Operating under Constant Load and Speed Conditions are introduced to provide supplementary data that can be combined or merged with existing bearing datasets to increase the amount of data available to researchers. This data utilizes various sensors such as an accelerometer, a microphone, a load cell, a hall effect sensor, and thermocouples to gather quality data on bearing health. By incorporating vibration and acoustic signals, the datasets enable both traditional and machine learning-based approaches for rolling-element bearing fault diagnosis. Furthermore, this dataset offers valuable insights into the accelerated deterioration of bearing life under constant loads, making it an invaluable resource for research in this domain. Ultimately, these datasets deliver high quality data for the detection and diagnosis of faults in rolling-element bearings, thereby holding significant implications for machinery operation and maintenance.
Towards Better Benchmarking Using the CWRU Bearing Fault Dataset. Mechanical Systems and Signal Processing. 169:108732, 2022
*Hendriks, J., Dumond, P., Knox, D.,
2022
This paper investigates the use of the Case Western Reserve University (CWRU) bearing dataset for benchmarking bearing fault diagnosis convolutional neural networks (CNNs) in a domain shift problem. The common method for using the CWRU dataset for demonstrating domain shift is described and a potential flaw is identified. It is argued that the accepted procedure of constructing training and testing datasets with different operating conditions does not constitute a useful domain shift problem since the same physical bearings exist in both training and testing sets. To remedy this while using the CWRU dataset, an alternative benchmarking framework is proposed that constructs training and testing datasets with independent sets of bearings. The original and the proposed benchmarking frameworks are compared by training a set of commonly cited diagnosis CNNs within each framework. The results indicate that the original framework allows CNNs to learn features related to specific bearings and may not be able to generalize for different bearings. It is also found that using existing state-of-the-art deep CNNs from other fields in machine learning research may currently present a more efficient option than developing custom CNN architectures for diagnosis when large machine fault datasets are unavailable.
Exploring the Relationship between Preprocessing and Hyperparameter Tuning for Vibration-Based Machine Fault Diagnosis Using CNNs. Vibration. 4(2):284-309, 2021
*Hendriks, J., Dumond, P.,
2021
This paper demonstrates the differences between popular transformation-based input representations for vibration-based machine fault diagnosis. This paper highlights the dependency of different input representations on hyperparameter selection with the results of training different configurations of classical convolutional neural networks (CNNs) with three common benchmarking datasets. Raw temporal measurement, Fourier spectrum, envelope spectrum, and spectrogram input types are individually used to train CNNs. Many configurations of CNNs are trained, with variable input sizes, convolutional kernel sizes and stride. The results show that each input type favors different combinations of hyperparameters, and that each of the datasets studied yield different performance characteristics. The input sizes are found to be the most significant determiner of whether overfitting will occur. It is demonstrated that CNNs trained with spectrograms are less dependent on hyperparameter optimization over all three datasets. This paper demonstrates the wide range of performance achieved by CNNs when preprocessing method and hyperparameters are varied as well as their complex interaction, providing researchers with useful background information and a starting place for further optimization.
bottom of page